Embedded Systems In Industrial Automation
embedded systems in Industrial automation can be defined as the process of delegation of repetitive human control functions to the equipment. Industrial automation is done using control systems such as PLC’s, computers, and microcontrollers to process and control machinery to help reduce the need for repetitive human intervention. Embedded systems help to automate the process by instructing the machines regarding how to produce a product or a component. Industrial Automation is used in almost every type of manufacturing industry such as textile, food/beverage, mining, metal, manufacturing, and many others.
Embedded systems act as a programmable operating system in larger systems that performs tasks such as controlling line speeds, driving motors, adjusting temperature, and networking equipment. The main purpose of the industrial embedded systems for industrial automation is to monitor and control the processes which will enable to improve overall efficiency and maximum performance in challenging and often requiring precision environments.
Industrial automation involves transferring repetitive tasks typically performed by humans to machines and equipment. This is accomplished using control systems like Programmable Logic Controllers (PLCs), computers, and microcontrollers.. These systems process and manage machinery to reduce the necessity for human intervention. Industrial embedded systems play an essential role in automating these processes by directing machines on how to produce various products or components. This kind of automation is widely implemented across numerous manufacturing sectors, including textiles, food and beverages, mining, metal manufacturing, and many others.
Embedded systems are designed to function as programmable operating systems within larger frameworks. They perform various tasks, such as controlling line speeds, driving motors, adjusting temperatures, and networking equipment. The primary purpose of these industrial embedded systems is to monitor and control processes, thereby enhancing efficiency and maximizing performance in environments that demand high precision.
The Evolution of Industrial Embedded Systems
Before the widespread adoption of industrial embedded systems, operators manually controlled and monitored machinery. This approach presented several challenges, such as time-consuming integration with existing control and monitoring systems, network infrastructure incompatibility, and inadequate support for extensive industrial setups requiring precise control to improve efficiency.
As companies have transitioned towards industrial automation, they have not only achieved greater operational efficiency but also reduced error rates, improved power efficiency, and enabled preventive maintenance. The data collected, processed, and analyzed by industrial embedded systems generate valuable insights. These insights allow operators to measure performance and concentrate on refining industrial processes.
Key Applications of Embedded Systems in Industrial Automation
- Machine Control
Industrial embedded system engineering services are vital for various industrial equipment. They perform specific tasks such as controlling robotic machinery, managing assembly line speeds, and regulating fluid flow rates. These systems significantly contribute to industrial automation by facilitating communication at the input/output level through programmable logic controllers. They integrate effectively with existing machine controls, utilizing automation software with proprietary numerical control and computer numerical control. By achieving a unified and centralized control architecture, industrial OEMs (Original Equipment Manufacturers) and manufacturing plants can lower maintenance costs and improve overall product quality.
- Machine Monitoring
Embedded software development capabilities are essential for industrial automation systems to monitor conditions in real-time. These systems control variables such as temperature, pressure, vibration, flow rate, and power. Data derived from sensors and other sources is stored in a centralized database or the cloud for real-time analytics. This information provides insights through reports, notifications, and dashboards, helping to reduce maintenance costs and minimize production losses.
Integration with IIoT and Advanced Electrical Design
In 2025, industrial embedded systems, the Industrial Internet of Things (IIoT), and advanced electrical design will combine to significantly improve industrial automation. IIoT allows smooth connectivity and real-time data sharing among devices, systems, and applications. This connectivity enables more accurate monitoring, control, and optimization of industrial processes.
Electrical design plays a crucial role in ensuring that industrial embedded systems are efficiently integrated into existing infrastructure. Proper electrical design guarantees compatibility, reliability, and safety of embedded systems within the industrial environment. By optimizing electrical design, companies can achieve smooth operation and maintenance of their automated systems.
Advantages of Industrial Automation with Embedded Systems
Better Efficiency: Automation of mundane operations increases productivity and reduces the number of human errors and smoothens the process
Cost Saver: Maintenance costs are reduced, as well as the downtime, which result in significant cost savings.
Product Quality: Consistent and precise control of processes enhances the quality of products significantly.
Real-Time Monitoring: Continuous monitoring and real-time analysis improves decision-making and operational efficiency two-fold.
Scalability: Embedded systems can easily be increased to meet the growing demands of industrial operations.
Industrial Embedded Systems in the Coming Future
The Evolution: Advancing technology and an increasingly complex industrial process will progress further this role of industrial embedded systems. Their future will be that of increasing sophistication to achieve even higher levels of automation and efficiency.
Real Examples of Industrial Automation
- Manufacturing Industry
Industrial embedded systems in the manufacturing sector are applied on assembly lines for control; they are used in managing robotic arms, including monitoring temperature and pressure production parameters, to ensure that products are made uniformly and meet quality requirements. Manufacturers can increase output, reduce waste and lower production costs by automating these tasks.
- Food and Beverage Industry
Industrial embedded systems in the food and beverage industry help monitor and control the conditions of processing to ensure quality and safety in food. It deals with things like temperature regulation in cooking, monitoring the pH levels in beverages, and tracking the flow of ingredients. Automation in this industry ensures that the quality of products is constant, in line with regulatory standards, and at its best efficiency.
- Mining Industry
Industrial integrated systems are employed in mining to control big equipment, measure the environment, and extract products. The system provides real-time data on equipment performance and environmental conditions, making mining safe and efficient. Automation reduces the risks of accidents and assists in the optimization of resource extraction and minimization of environmental impacts.
- Metal Manufacturing Industry
Industrial embedded systems in metal manufacturing control the processes of casting, forging, and rolling. It keeps checking and adjusting parameters like temperature, pressure, and speed for quality production of metal products. It improves product quality and raises production efficiency while reducing energy consumption.
The Role of IIoT and Electrical Design in Industrial Automation
Industrial embedded system capability will be highly promoted with the integration of IIoT and advanced electrical design in industrial automation. IIoT supports the analysis of the real-time data for effective data analysis and decision-making in actual time. Electrical design of such systems ensures seamless integration, ensuring reliability and good performance in the existing infrastructure.
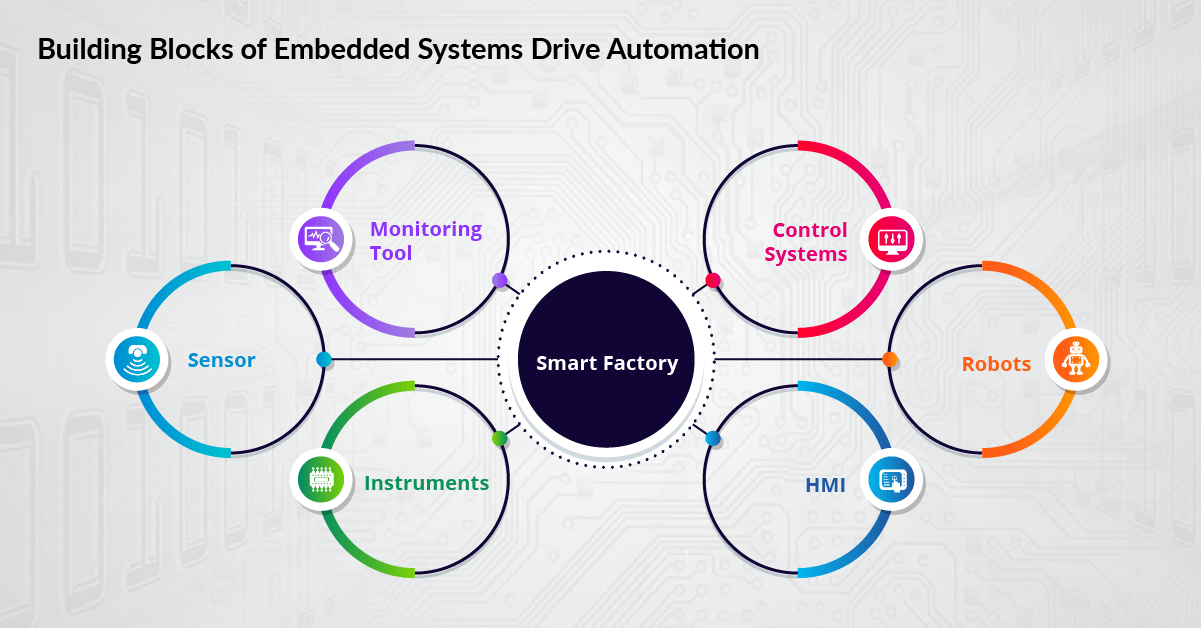
Embedded Systems have 2 Key Uses:
Machine Control – Embedded system engineering services are used in various industrial equipment to perform specific tasks such as controlling robotic machinery, controlling assembly line speeds, and controlling fluid flow rates. Their use has contributed immensely to industrial automation. Communicating at the input/output level via programmable logic controllers, these embedded systems integrate well with the existing machine controls which leverage automation software with proprietary numerical control and computer numerical control. Industrial OEMs (Original equipment manufacturers) and manufacturing plants can achieve a unified and centralized control architecture by reducing the maintenance costs and contributing to the overall product quality.
Machine Monitoring – Embedded Software development capabilities are used by industrial automation systems that help them to monitor systems conditions in real-time by the use of controlled monitoring of variables such as temperature, pressure, vibration, flow rate, power, and more. The data derived from the sensors and other different data sources is stored in a centralized database or in the cloud for real-time analytics which will help in providing the insights through reports, notifications, and dashboards. This helps in reducing maintenance costs and to cut any production losses.
Conclusion
Industrial automation powered by embedded systems is likely to be the efficiency and precision coupled with cost-effectiveness in the manufacturing process. IIoT and electrical design advancement will further progress the capability of these systems, making industrial operations more streamlined and productive. Looking into 2025, the role of industrial embedded systems will continue to grow and provide innovative solutions for the changing industry needs.
Industrial embedded systems, industrial automation, IIoT, and advanced electrical design are all changing the face of how things run in industries, giving extraordinary levels of efficiency, precision, and cost savings. The future of industrial automation is shining bright with endless opportunities for improvement and innovation.
Prior to the application of the embedded systems for industrial machines, there was a manual intervention by the operators which helped to control and monitor the machines. There were many issues such as time-consuming integration with the existing control and monitoring systems, network infrastructure incompatibility, and was not able to support a giant industrial setup requiring precision control to improve efficiency.
Many companies are moving towards industrial automation as it helps in achieving not only greater efficiency but also a much lower error rate, higher power efficiency, and preventive maintenance. The data that is gathered, processed, and analyzed by the embedded computers is used to create valuable insights. This insight helps the operators to measure performance and focus on improving the industrial processes.
Avench is one of the leading embedded companies in the United States, to know more information about embedded systems and embedded product design please subscribe to our blog, and for any sales queries, wait for no further contact us at +1 (775) 404-5757. You can also email us at sales@avench.com we would be happy to assist you.