In an age of multiple and massive innovations, obsolescence become the major obsession – Marshall McLuhan
Obsolescence management is a coordinated effort aimed at leading and controlling a product in terms of obsolescence. The primary objective of obsolescence management is to prevent costly resolutions when obsolescence issues arise. Detailed planning can reduce the impact of obsolescence and its potentially high costs. In simple terms, the key elements of the obsolescence management strategy include:
- An understanding of the current and future risk to the components within a system
- Understand the current and future obsolescence risk
- Put steps in place to mitigate known risk
- Reduction on expensive reactive obsolescence resolutions
- Reduce the impact of obsolescence on:
- Capability
- Cost
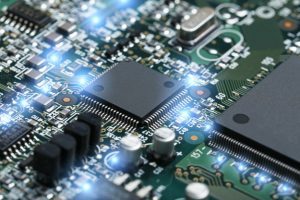
Avench Process
-
Collect Component Information
-
Check Availability
-
Quantify Risk Assessment
-
Advice on No Stock & Obsolescence
-
Risk Mitigation Plan
-
Periodic Reporting
Workflow: Obsolescence Management Process
Product Information
Gather product details like Product ID, Description, Annual volume, Product roadmap, Authorized vendors and Current manufacturing requirements Bill of Material Design files: Schematics, PCB and Gerber
Database Management
Review BOM for correctness, Conversion of BOM to database
Lifecycle Management
Stock check and Life cycle status at Digikey and Mouser, Components life cycle status report generation, Email notification to stake holder
Risk Assessment
High Risk (Full risk analysis required for these components. Mitigation strategies should be decided accordingly), Medium Risk (The components contained in this category should be monitored, so that any obsolescence issue can be managed proactively), Low Risk (These are the low-risk items from a obsolescence stand point)
Risk Mitigation
Alternate component selection, Last time buy, PCB Re-spin, Identify alternate vendors
Report
Availability – Obsolete/not in stock/discontinued/active, Alternate components, Risk level of components (High, Medium, Low), Health Analysis (Obsolete, EOL, Alternate components and No match)
Approval
Final Report will be shared to the client design team for approval, particular part number can be approved or rejected. Approved: Spread sheet will be maintained with all approved components. Not Approved: In comments details can be mentioned reason for rejection.
Final BOM
Final BoM in standard document format
Check Obsolescence Periodically
Check the components obsolescence periodically for the defined period of time. Share the reports periodically. Take appropriate measure to solve the components obsolescence proactively focused to client BOM.
What makes us different?
Detailed Market Research
Experienced Development Team
Technical Support
Timely Execution