The oil and gas industry is one of the pillars of our global economy, powering industries and communities worldwide. However, its complexity and hazardous working conditions pose significant challenges. The industry is under constant pressure to improve efficiency, reduce operational costs, and enhance safety. We will see how IIOT in oil and gas industry operates to enhance safety and efficiency. This technology involves the use of interconnected devices, sensors, and systems that are integrated into oil and gas operations to monitor and control various processes.
In this article, we’ll explore how IIOT is transforming the oil and gas industry and the benefits and challenges of implementing it. So, let’s dive in!
The IIOT development has led to an enhancement in safety in the oil and gas industries. From predictive maintenance to real-time data analysis, from remote monitoring to safety monitoring, IIOT has transformed the industry.
For example, IIOT sensors can monitor and control the temperature and pressure of pipelines, helping to prevent leaks and damage. IIOT applications can also be used to monitor the health of equipment and predict when maintenance is needed, reducing downtime and maintenance costs.
Implementing IIOT in Oil and Gas Industry: Pros
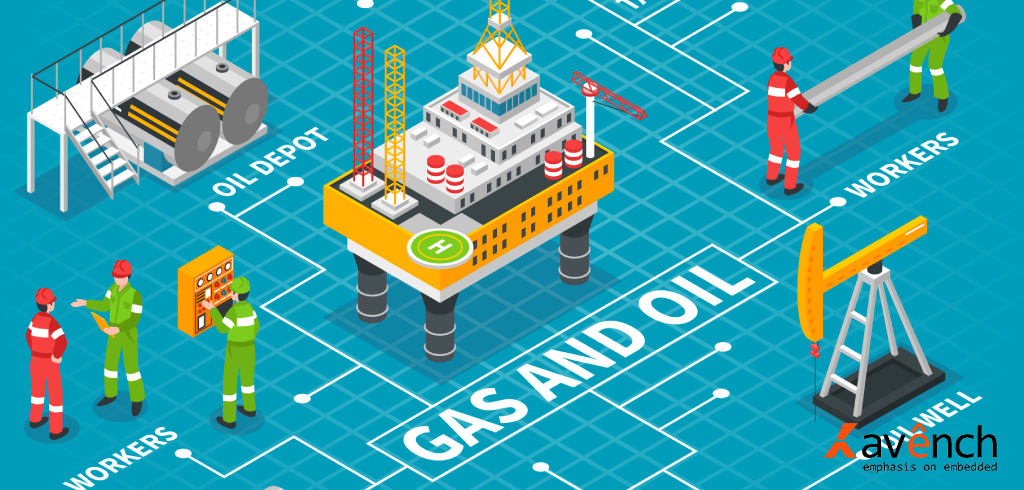
The benefits of implementing IIOT in oil and gas are significant. Improved efficiency, reduced downtime, increased safety, and enhanced asset management are just a few of the benefits. IIOT technology provides real-time data that can be used to optimize processes and improve decision-making, leading to improved efficiency and reduced costs. IIOT also provides increased visibility into the operations, allowing for more proactive and predictive maintenance and reducing downtime and maintenance costs. Additionally, IIOT can help enhance safety by monitoring working conditions and alerting workers to potential hazards. We’ll look at some of the pros in this section.
1. Monitoring, tracking, and maintaining assets
The oil and gas refineries must be inspected regularly. Sometimes, the faculty might not be able to investigate the refineries and monitor their maintenance. Setting up a piece of equipment and connecting it to an IoT network can help reduce the need for manual inspections. Pumps, pipes, filters, valves, and other parts can all have sensors installed on them to keep track. This makes it possible for technicians to keep an eye on every mechanical component of the refinery’s machinery. Thus, the IIoT enables real-time asset tracking and monitoring, which is not possible with manual inspections.
Additionally, the IIoT network’s data collection enables the early detection of potential problems. Therefore, using the data, technicians can quickly locate the precise location where the anomaly was noticed and take the appropriate action.
2. Administration of data
The IIOT network enhances data management by integrating information from various assets through industrial protocols, reducing costs, and improving profitability. Data is aggregated in the cloud, utilizing techniques like edge analytics for valuable insights.
Two critical elements influence effective decision-making: the requirement for precise data and the departure of seasoned employees as a result of layoffs or restructuring. Data analysis and remote monitoring enable efficient asset management and maintenance programs for streamlined rig operations.
Real-time data from the IoT network improves extraction and drilling strategies. Implementing monitoring and maintenance procedures reduces unnecessary expenses, and the automated network delivers essential data to employees’ systems, eliminating the need for extensive on-site investigations.
3. Logistics, transportation, and supply chains
The IIoT offers significant benefits in the supply chain and logistics sectors. Data collected from various network touchpoints enables managers to optimize procurement and supply and identify best practices.
Connectivity challenges arise during the transportation of oil and gas through pipelines and ships, often necessitating reliance on satellite communication for data transmission. Monitoring the condition of pipelines and ships can also be challenging. To address this, Low-Power wide-area networks (LPWAN) can be deployed in remote pipeline areas. Wired and wireless networks can be established along transportation routes to gather and transmit data to the cloud via satellite connectivity. This ensures that office staff receive reliable and accurate information, facilitating more efficient oil deliveries.
4. Safety and Well-being
IIoT plays a pivotal role in enhancing employee safety and reducing carbon emissions in oil and gas operations, particularly in remote and hazardous locations. Connected sensors provide real-time data, enabling better monitoring of on-site conditions. Predictive maintenance and remote equipment monitoring help minimize machine breakdowns, while sensor-captured data and surveillance systems ensure adherence to the highest safety standards. Wearable devices with location trackers further enhance worker safety by enabling quick response to emergencies, ultimately leading to a decrease in accidents and fatalities.
Delving into Some Challenges
Implementing IIOT technology in the oil and gas industry also comes with challenges. A few are listed below,
1. Data Security and Privacy: IoT devices produce sensitive data, making them susceptible to cyberattacks. It is crucial to implement robust cybersecurity measures, conduct regular audits, and provide ongoing employee training. Additionally, utilizing blockchain technology can offer secure data storage solutions.
2. Integration Issues: Integrating IoT with legacy systems can be complex and challenging. To address this, begin by assessing existing systems, carefully planning the integration process, leveraging middleware solutions, and ensuring compatibility with industry-standard protocols.
3. Data Overload: Operational inefficiencies may result from the massive amount of data generated by the Internet of Things. This can be lessened by using edge computing for analytics, machine learning, and data preprocessing. It also makes it possible to extract insightful information right away and lowers the overhead associated with data transmission and processing.
4. Scalability and Maintenance: Managing a growing number of IoT devices can become complex and costly. To address this issue and ensure the longevity and efficacy of the devices, predictive maintenance algorithms, remote monitoring systems, and early scalability planning are required.
5. Skilled Personnel Shortage: The need for more IoT expertise in the workforce can be a stumbling block. Invest in training for your current staff to address this problem, work with academic institutions to develop IoT talent, and, if needed, consider outsourcing particular tasks.
6. Regulatory Compliance: Meeting industry regulations with IoT implementations can be intricate. The key is to engage with regulators, develop a comprehensive compliance strategy, and select IoT solutions that come equipped with built-in compliance features to simplify adherence to the necessary rules and standards.
7. Power and Connectivity in Remote Locations: Remote locations often lack consistent power and connectivity. Use low-power IoT devices, investigate renewable energy sources like solar or wind, and make use of long-range communication technologies to get around this problem and ensure IoT functionality even in the most remote locations.
Case study: MFL Pipeline Inspection Gauge
Avench Systems developed an investigation gauge for the US/Canada-based oil and gas manufacturer that detected cracks and corrosion inside an oil and gas pipeline by using a technology called “Magnetic Flux Leakage”. Using this technology, a strong magnetic field has been developed in the cross-section of the pipe, and an array of sensors have reported flux leakages and magnetic losses.
We could deliver the project promptly, and the trials were a good hit too. Our customer felt satisfied with the field trials, that we were given additional requirements, and that we assured complete client satisfaction.
Download Case Study: https://avench.com/case-study/pipeline-investigation-gauge/
Arriving at the Closure
Overall, the Industrial Internet of Things (IIOT) has the potential to revolutionize the oil and gas industry by improving efficiency, enhancing safety, and reducing operational costs. However, the successful adoption of IIOT requires careful planning, investment in the right technology, and addressing various challenges such as cybersecurity risks and data management. At Avench, we possess expertise in embedded systems and innovative engineering solutions, which allows us to bridge the gap between technology and the specific needs of the oil and gas industry. We can help companies implement IIOT solutions that are robust, reliable, and optimized for their unique needs. So, if you’re looking to take advantage of IIOT in the oil and gas industry, consider partnering with us to unlock the full potential of this transformative technology.
For more details contact the best embedded software development company.