The concept of Industry 4.0 is shaping modern manufacturing in ways that were once hard to imagine. At the core of this transformation is the Internet of Things (IoT). Together, IoT and Industry 4.0 are driving the shift toward smart manufacturing. By enabling real-time data collection and advanced analytics, IoT plays a crucial role in optimizing production processes, reducing downtime, and improving overall operational efficiency. But what exactly is IoT in Industry 4.0, and why is it such a game-changer for manufacturing?
What is IoT in Industry 4.0?
The Internet of Things in Industry 4.0 refers to the interconnected network of sensors, devices, and systems embedded in manufacturing processes. These devices communicate with each other and the central systems to provide real-time data on every aspect of production. IoT is central to Industry 4.0, allowing manufacturers to monitor machine health, track inventory, and optimize energy usage, all in real-time.
This interconnected network not only allows data collection but also facilitates predictive maintenance, remote monitoring, and automation. When machines are continuously monitored for performance and efficiency, manufacturers can prevent costly breakdowns, reduce maintenance costs, and ensure the smooth functioning of operations.
Role of IoT in Industry 4.0
IoT plays a significant role in revolutionizing manufacturing. It integrates the physical and digital worlds, leading to intelligent and interconnected production environments. For example, a smart factory equipped with IoT can automatically adjust machinery based on real-time data from the production line. This reduces waste, boosts efficiency, and improves quality.
In an Industry 4.0 setup, IoT devices provide a continuous stream of data that can be analyzed to uncover inefficiencies, predict machine failures, and optimize the use of resources. This data-driven approach enhances decision-making and allows manufacturers to respond swiftly to changing conditions on the production floor.
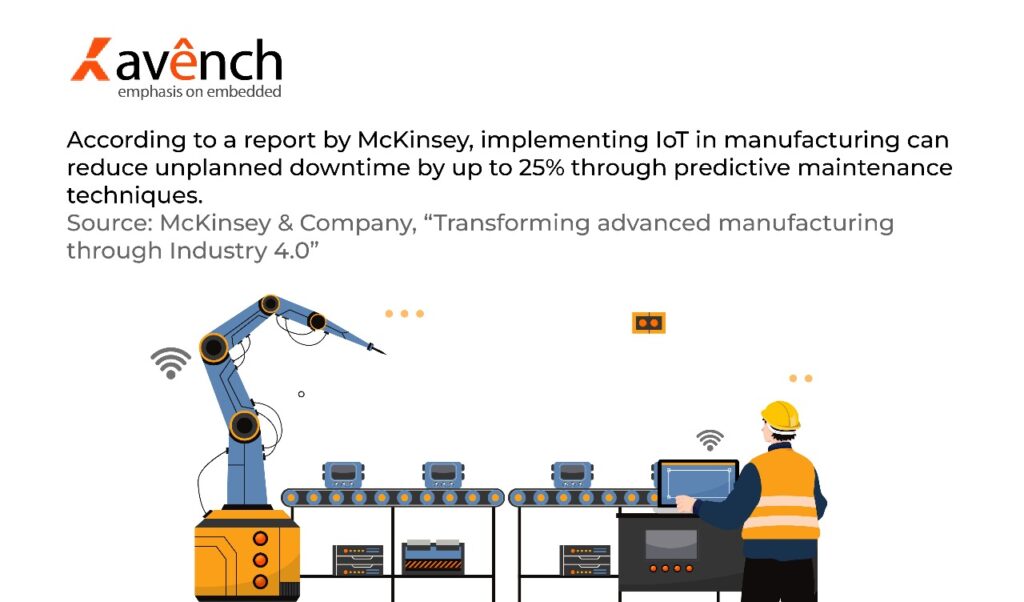
Moreover, the role of IoT extends beyond just monitoring. It enables automation by integrating robots and automated systems into the production process. These machines can communicate with one another and adjust their operations based on real-time inputs, further increasing production speed and accuracy. As a result, manufacturers can produce more in less time while maintaining high levels of precision.
Applications of IoT in Industry 4.0
The applications of IoT in Industry 4.0 are wide-ranging. One of the most notable is predictive maintenance. IoT sensors can monitor equipment for signs of wear and tear, predicting when maintenance is needed before a failure occurs. This minimizes downtime and keeps production running smoothly.
Another key application is inventory management. IoT in industrial automation devices track raw materials, finished goods, and everything in between. This data helps manufacturers optimize their supply chain, ensuring they always have the right materials in the right place at the right time.
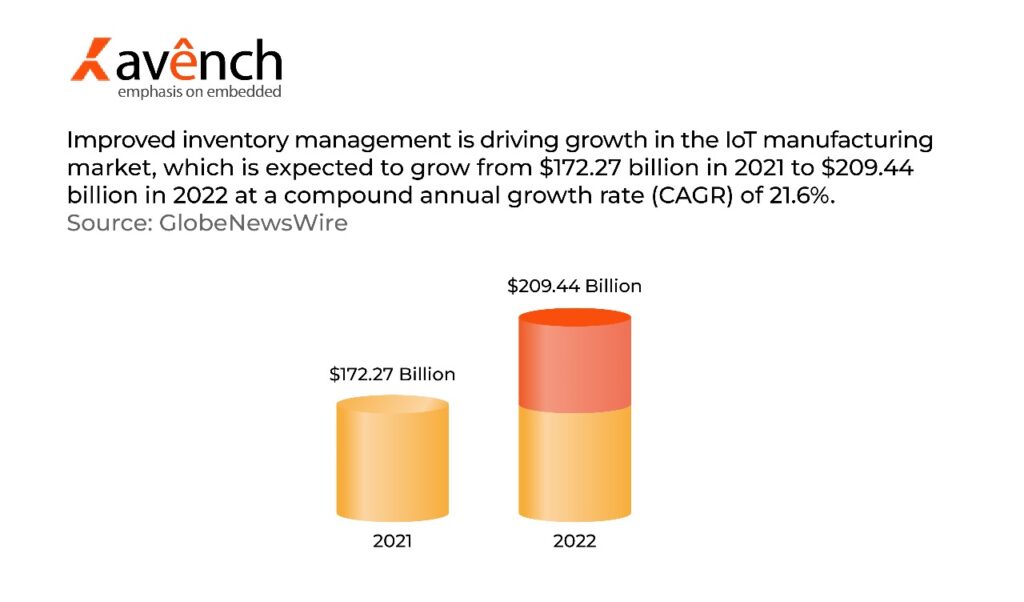
Energy efficiency is another area where IoT shines. By monitoring energy consumption in real-time, manufacturers can identify wasteful practices and make adjustments to reduce their overall energy use. This not only saves money but also reduces the environmental impact of manufacturing operations.
In addition to these applications, IoT enhances quality control by allowing manufacturers to monitor product quality throughout the production process. IoT-enabled systems can detect defects early, reducing the need for costly rework and ensuring that only high-quality products make it to market.
Challenges in Implementing IoT in Manufacturing
While the benefits of IoT in Industry 4.0 are substantial, implementing IoT technology is not without its challenges. One of the primary concerns is data security. With so many devices interconnected and sharing data, ensuring the security of that data becomes paramount. Manufacturers must invest in robust cybersecurity measures to protect their systems from cyber threats.
Another challenge is the cost of implementation. Although IoT systems can lead to long-term savings, the initial cost of purchasing and installing the necessary hardware and software can be high. Manufacturers must carefully weigh these upfront costs against the potential benefits when deciding whether to implement IoT technology.
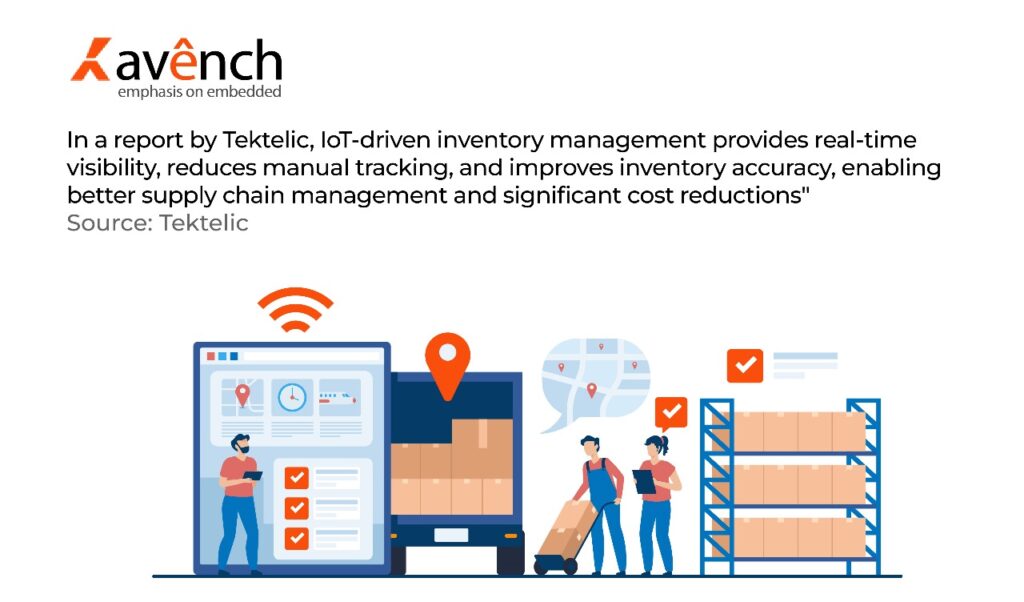
Furthermore, integrating IoT into existing manufacturing systems can be complex. Legacy systems may not be compatible with modern IoT devices, requiring costly upgrades or replacements. Additionally, employees need to be trained to operate and manage these new systems effectively.
Looking Ahead: The Future of IoT in Industry 4.0
As more manufacturers recognize the potential of IoT in Industry 4.0, its adoption is expected to continue growing. With advancements in artificial intelligence and machine learning, IoT systems will become even more intelligent, capable of learning from the data they collect and making decisions without human intervention.
One area where IoT is poised to make a significant impact is in the development of “smart factories.” These fully automated factories will be able to operate with minimal human oversight, with IoT systems monitoring every aspect of production and making real-time adjustments to optimize performance.
In addition, 5G networks will play a crucial role in enabling faster and more reliable communication between IoT devices. With the ultra-low latency offered by 5G, IoT systems in Industry 4.0 will be able to react to changes on the production line instantly, further improving efficiency and reducing downtime.
Final Thoughts on the IoT and Industry 4.0 Synergy
The integration of IoT into Industry 4.0 has transformed the way manufacturers operate. By connecting devices, machines, and systems, IoT provides manufacturers with real-time data that can be used to optimize processes, improve product quality, and reduce costs. While there are challenges to overcome, the potential benefits of IoT in Industry 4.0 far outweigh the obstacles.
As technology continues to evolve, the relationship between IoT and Industry 4.0 will only grow stronger, paving the way for smarter, more efficient manufacturing processes that will shape the future of the industry. For manufacturers willing to invest in IoT technology, the rewards are clear: increased productivity, reduced downtime, and a more resilient production process.
Avench is one of the leading embedded companies in bangalore, to know more information for any sales queries, wait for no further contact us at +1 (775) 404-5757. You can also email us at sales@avench.com, or fill the query form in a website.